This week we were highlighted on Jet TV Action News in Erie! http://yourerie.com/fulltext?nxd_id=272302 The video is posted on our
website.
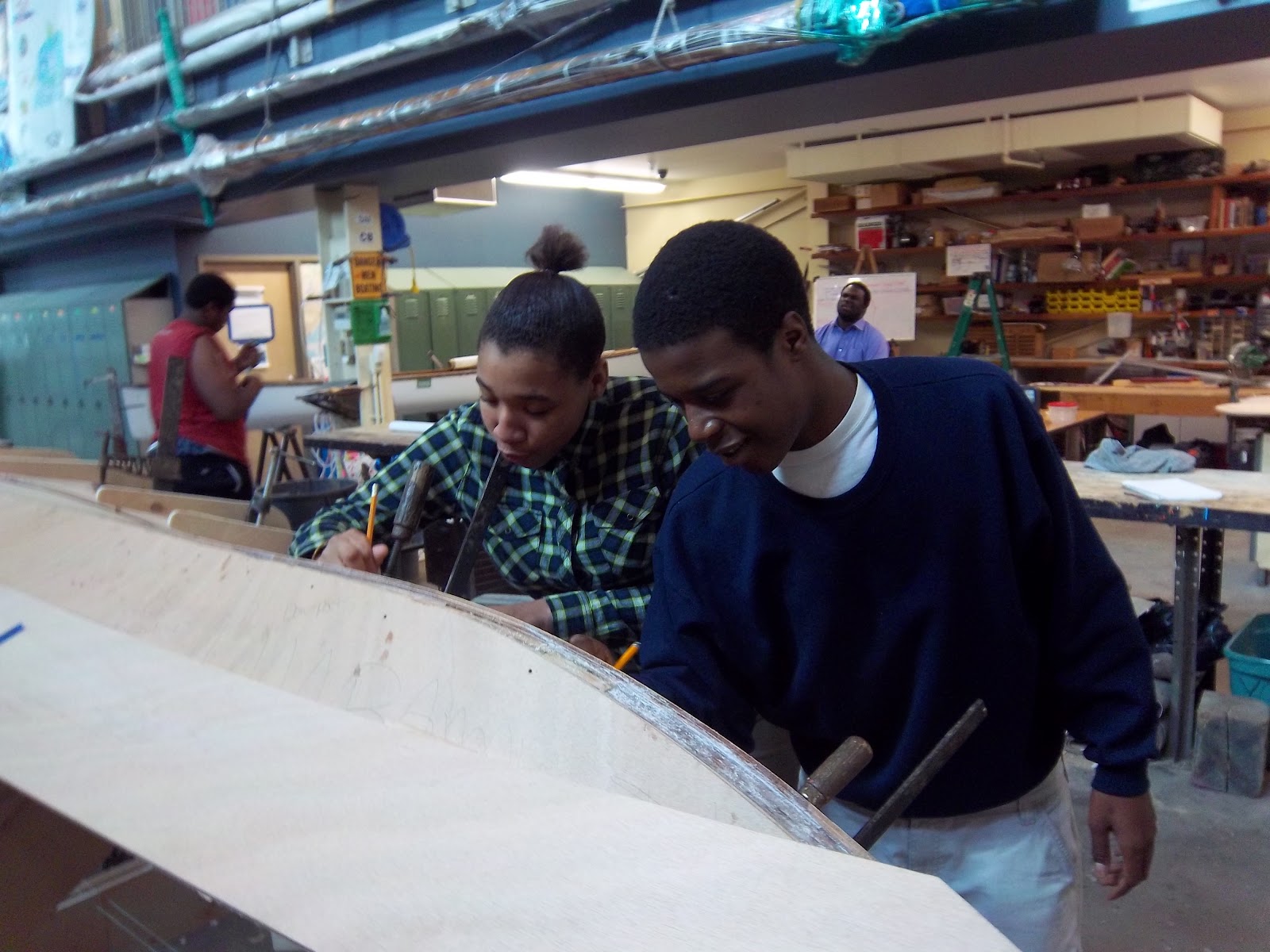 |
We marked where the epoxy needed to go on plank 2 for the starboard side. |
 |
Spreading glue on plank two. |
 |
We clamped plank 2 on to the port side, while we waited for the epoxy to dry.
( We used over 40 clamps! )
|
 |
We used epoxy to glue plank 3 together. |
 |
We used a spoke shave to plane a bevel in the land.
The land is the area that the next plank would be glued on to.
|
 |
Upper left, Jet TV is here talking to our Executive Director, Rich Eisenburg. |
 |
We used a rasp to bevel the frame.
|
We gave it 100 percent effort to build the boat to this point and we would like to thank Jet TV Action News for coming to our school and observing the work we have done so far. If anyone else is interested in stopping by please let us know. We hope we were a inspiration to everybody that has seen the boat so far.
Thank you.